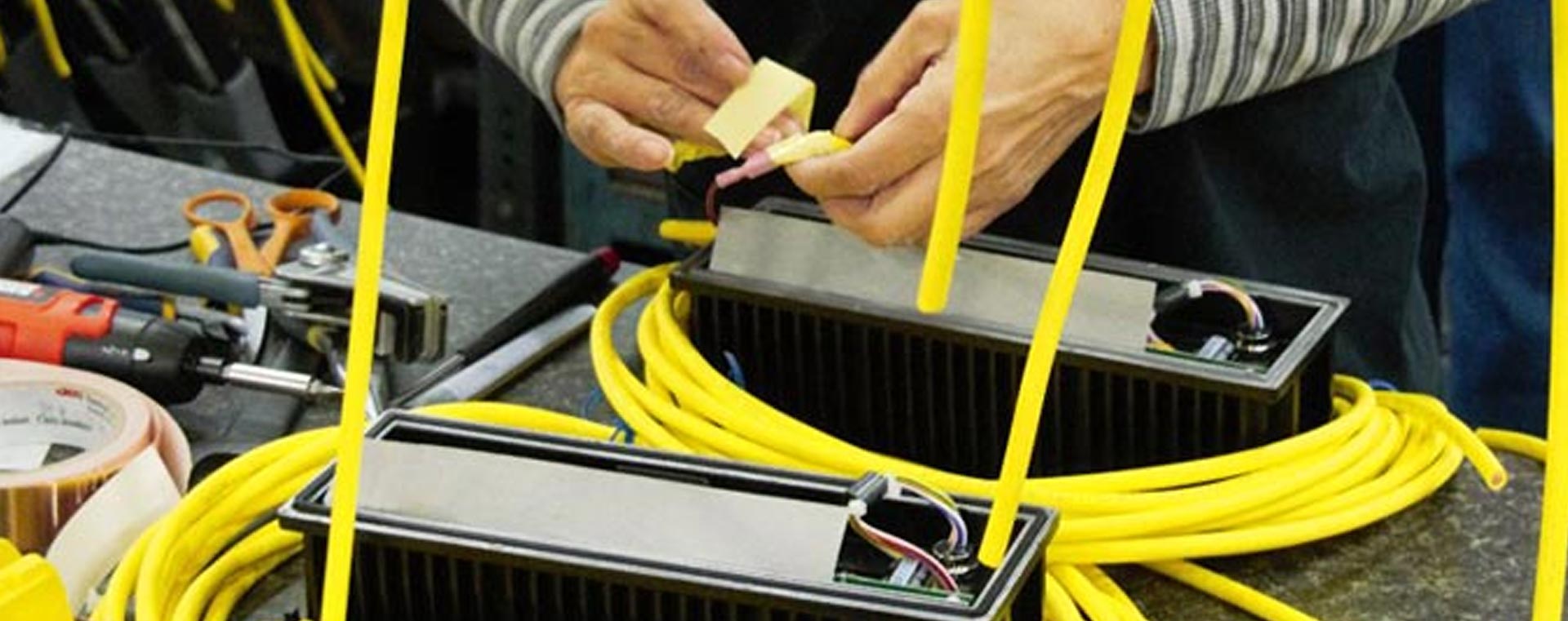
Precision Assembly & Secondary Operations for Injection Molded Components
PRECISION
EXPERT ASSEMBLY
FOR COMPLEX COMPONENTS
30%
PRODUCTION TIME REDUCTION
WITH INTEGRATED ASSEMBLY
Full Service
HOT STAMPING & DECORATION
FOR ENHANCED AESTHETICS
Comprehensive Component Assembly Solutions
Our expert assembly team integrates multiple components into finished products with exceptional accuracy and efficiency. Whether you need simple snap-fit assemblies or complex multi-component manufacturing, our precision assembly services ensure consistent quality across high-volume production runs. By combining injection molding and assembly services under one roof, we reduce production time by up to 30% while maintaining tight tolerances and exceptional quality control throughout the entire manufacturing process.
Precision Assembly
Our skilled assembly team delivers high-precision component assembly with exceptional attention to detail. Through careful planning and specialized training, we ensure precise alignment and consistent quality across production runs of any size, maintaining tight tolerances and meeting exact specifications.
Manual Assembly Operations
Our skilled assembly technicians excel at complex manual assembly processes requiring dexterity and attention to detail. Each technician undergoes extensive training to ensure consistent quality for components that require careful handling and specialized assembly techniques.
Multi-Component Integration
We excel at integrating multiple components and materials into finished assemblies. Our assembly capabilities include snap-fit connections, threaded fastening, adhesive bonding, and various mechanical joining methods to create durable, high-quality assembled products.
Advanced Decorative Finishing for Injection Molded Parts
Our hot stamping and decorative finishing services enhance the visual appeal and functionality of your plastic components. Using advanced hot stamping technology, we can add vibrant metallic finishes, distinctive patterns, and precise branding elements to your plastic parts with exceptional adhesion and durability.
Norco's hot stamping services offer superior aesthetics with consistent quality across high-volume production runs. Our specialized equipment applies decorative foils at precisely controlled temperatures and pressures to achieve optimal transfer and adhesion. Hot stamping creates a durable, scratch-resistant finish that withstands demanding environments while providing superior visual impact.
Whether you need branding elements, operating instructions, functional graphics, or purely decorative patterns, our hot stamping capabilities transform ordinary plastic components into premium, attention-grabbing products. This value-added service integrates seamlessly with our molding and assembly operations, creating a streamlined production process that enhances your components while maintaining efficient turnaround times.
Benefits of Hot Stamping & Decoration
- Superior metallic finishes with vibrant, eye-catching appearance
- Excellent durability with scratch and chemical resistance
- Precise application with exceptional edge definition
- Multiple colors and patterns available for custom designs
- Environmentally friendly alternative to liquid painting
- Cost-effective for both high and low volume production
- Consistent quality across large production runs
- Compatible with a wide range of plastic materials
Common Decorative Finishing Applications
- Brand logos and identifiers
- Product information and warnings
- Control panel markings
- Serial numbers and barcodes
- Metallic accents and highlights
- Wood grain and textured finishes
- Graphic patterns and designs
- Functional markings and scales
Equipment & Technology
Advanced Assembly & Secondary Operations Machinery
Our facility features state-of-the-art assembly equipment and technology designed to deliver precision results with maximum efficiency. We've invested in specialized assembly machinery and precision manual assembly stations, all calibrated to meet exact specifications and tight tolerances.
For hot stamping and decorative operations, we utilize advanced foil application systems with precise temperature and pressure controls. This equipment enables consistent, high-quality decoration across production runs of all sizes. Our technology is versatile enough to accommodate different substrate materials, component geometries, and design requirements.
Quality control is integrated throughout our assembly and secondary operations, with digital measurement tools and optical inspection systems verifying dimensions and appearance at key production stages. This comprehensive quality assurance approach ensures consistent results that meet or exceed specifications while maintaining efficient throughput for your production schedule.
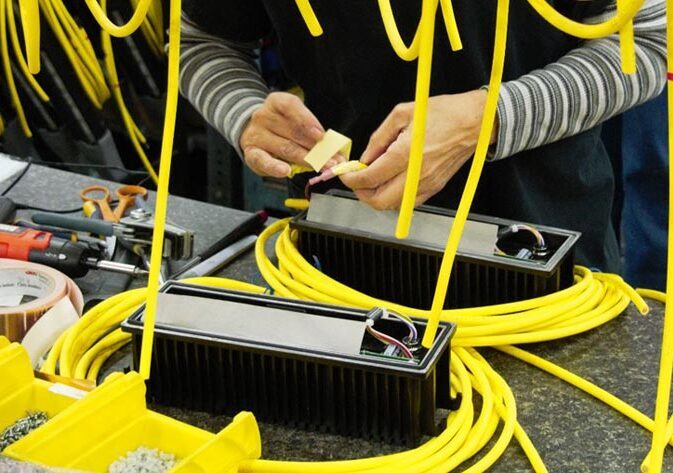
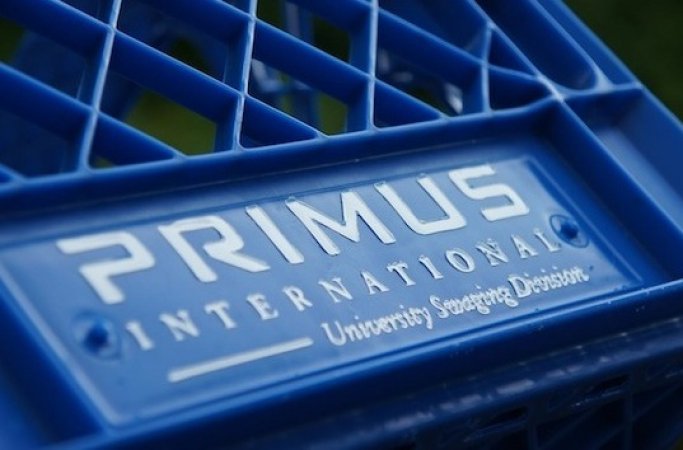
Assembly & Secondary Operations for Multiple Industries
Norco Plastics provides comprehensive assembly services and secondary operations for a diverse range of industries. Our assembly capabilities accommodate everything from simple snap-fit connections to complex multi-component products requiring precision alignment and integration. With decades of experience in plastic component assembly, we understand the specific requirements for each industry and ensure that assembled products meet or exceed quality standards while maintaining cost-effectiveness.
Our decorative finishing services enhance plastic components with precise branding, functional markings, and aesthetic elements that improve product value and appeal. We work closely with clients to understand their unique requirements, providing tailored assembly and finishing solutions that combine efficiency with exceptional quality. Whether you need simple mechanical assembly or complex integrated components with decorative elements, our team delivers consistent, reliable results across production runs of any size.
Consumer Products
Assembled housewares, appliance components, and retail product assemblies with decorative finishes and branding elements.
Automotive
Dashboard components, control interfaces, and interior trim assemblies with precise functional markings and decorative elements.
Medical Devices
Non-invasive medical product assemblies with clear operating instructions and precise calibration markings.
Construction
Building product assemblies, component systems, and infrastructure elements requiring durability and functional markings.
Frequently Asked Questions About Assembly & Secondary Operations
Get answers to common questions about our assembly and secondary operations services. If you need additional information, our team is ready to assist with your specific requirements.
What is the difference between primary and secondary operations?
Primary operations refer to the initial manufacturing process such as injection molding, where raw plastic material is formed into components. Secondary operations are the subsequent processes performed on these molded parts, including assembly, hot stamping, painting, and other finishing processes. Secondary operations enhance functionality, appearance, or prepare components for final use.
Can Norco assemble components they didn't manufacture?
Yes, Norco can provide assembly services for components we did not manufacture. While there are significant advantages to having us handle both injection molding and assembly (such as streamlined logistics and consistent quality control), we have the expertise and equipment to assemble components from multiple sources. Our team will work with you to ensure all parts meet specifications before assembly.
What decoration options are available for plastic parts?
We offer decoration options for plastic parts, including hot stamping and labeling. Hot stamping provides metallic finishes, textures, and patterns with excellent durability. Our team can help determine the optimal decoration method based on your part geometry, material, and design requirements.
What industries typically require assembly services?
Assembly services are utilized across numerous industries including consumer products, automotive, medical devices, electronics, construction, and industrial equipment. Any industry that requires finished products composed of multiple components can benefit from professional assembly services. Our expertise spans these diverse sectors, providing tailored assembly solutions that meet industry-specific requirements and standards.
How does assembly affect the total cost of production?
While assembly adds an additional step to the manufacturing process, consolidating molding and assembly with a single vendor often reduces overall production costs. This approach eliminates shipping between facilities, reduces handling damage, streamlines quality control, and minimizes administrative overhead. Our integrated approach typically results in 15-30% lower total production costs compared to using separate vendors for molding and assembly.
What quality control measures are used during assembly?
Our assembly operations include comprehensive quality control measures such as in-process inspections, first article approvals, dimensional verification, functional testing, and final visual inspection. We use precision measurement equipment including coordinate measuring machines (CMM) with accuracy to ±0.0001 inches. Each project has a customized quality plan that ensures assembled products meet all specifications and performance requirements.
Need more information about our assembly and secondary operations?
Contact Our Assembly Team