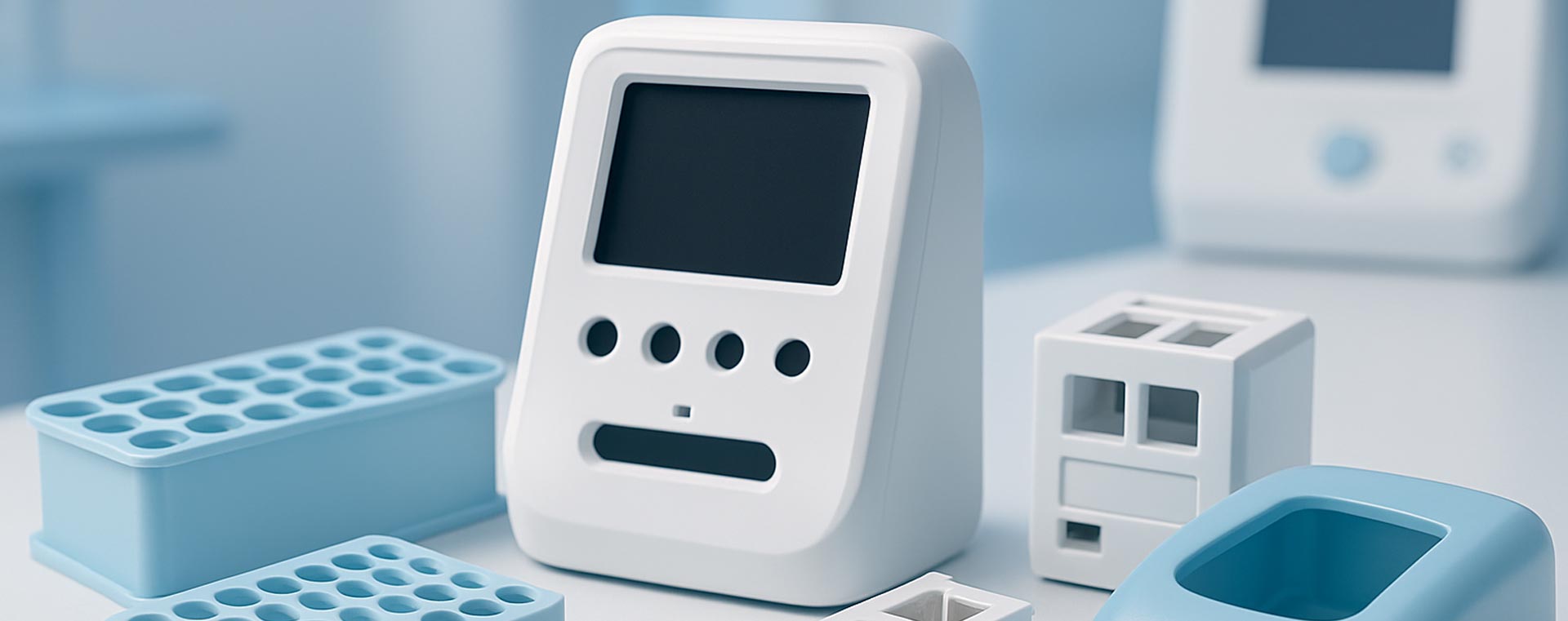
Medical Device & Healthcare Plastic Component Manufacturing
Our Southern California facility is equipped with advanced technology, including the Brown and Sharpe CMM for precision measurements to ±0.0001 inches, enabling us to maintain the tight tolerances specified for healthcare plastic components. As experienced medical injection molding companies, our capabilities extend from prototype development through high-volume production, supported by documentation systems that provide the traceability needed for your components.
With over 50 years of manufacturing experience, Norco Plastics delivers the stability and expertise that medical device manufacturers value. Our team understands the requirements of healthcare applications and can implement your specified protocols for material handling, process control, and consistent production of the medical plastic components you design.
±0.0001"
PRECISION MEASUREMENT
FOR MEDICAL COMPONENTS
100%
BATCH TRACEABILITY
WHEN REQUIRED
Medical-Grade
MATERIALS PROCESSING
PER YOUR SPECIFICATIONS
Meeting the Exacting Standards of Medical Device Manufacturing
Medical device manufacturing presents unique challenges that demand specialized expertise and precision manufacturing capabilities. At Norco Plastics, we understand the critical nature of healthcare applications and have developed solutions to address the manufacturing requirements of the medical industry. Our approach combines advanced technology with quality control systems to deliver components according to our customers' specifications.
Regulatory Compliance & Documentation
Medical devices require comprehensive documentation to meet regulatory standards. We can provide detailed documentation for the components we manufacture according to your specifications to support your regulatory processes. The responsibility for regulatory compliance remains with you as the product designer and owner.
Strict Tolerance Requirements
Medical components often require precision measurements to ensure proper fit and function. Our Brown and Sharpe CMM technology delivers accuracy to ±0.0001 inches, allowing us to manufacture to the tight tolerances specified in your designs for medical applications.
Material Selection Guidance
Healthcare applications require materials that are safe for human contact and meet specific performance characteristics. We can recommend USP Class VI polymers, medical-grade polycarbonates, and antimicrobial compounds based on your requirements. The final material selection decision and responsibility for biocompatibility remain with you, particularly for applications with potential regulatory implications.
Consistency & Traceability Demands
Medical manufacturing requires complete traceability from raw material to finished component. Our comprehensive batch tracking system maintains detailed records of every production parameter, material lot, and quality verification step. This enables rapid response to any quality concerns and supports complete documentation for regulatory compliance. Every component we manufacture is fully traceable throughout its lifecycle, providing the documentation trail essential for medical device manufacturers.
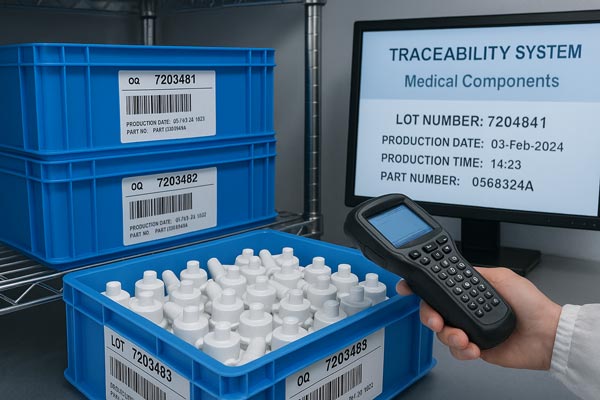
Non-Invasive Medical Components and Healthcare Products
Norco Plastics specializes in precision manufacturing of non-invasive medical components that maintain the highest standards of quality and consistency. Our injection molding capabilities are perfectly suited for the exacting requirements of healthcare applications, delivering components with exceptional dimensional accuracy, clean finishes, and reliable performance.
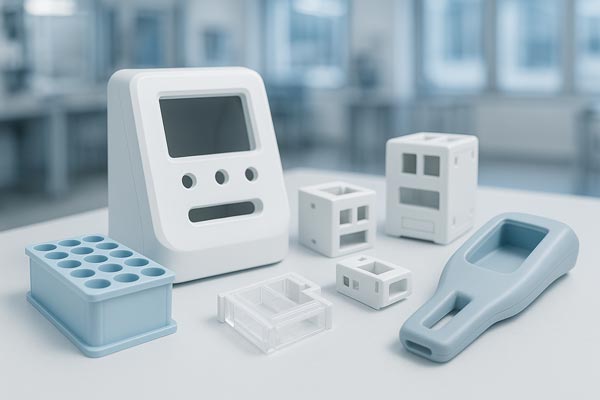
Key Medical & Healthcare Applications
Diagnostic Equipment Components
Precision housings, interfaces, and structural components for diagnostic instruments requiring exceptional dimensional stability and clean finishes.
Medical Sample Trays and Containers
Custom-designed storage solutions for laboratories and healthcare facilities, with precise compartment sizing and sterile surface finishes.
Healthcare Facility Equipment Parts
Durable components for hospital and clinical equipment with antimicrobial materials and ergonomic designs for healthcare environments.
Medical Device Housings and Enclosures
Protective enclosures for sensitive electronic equipment with precise tolerance control and specialized medical-grade materials.
Handheld Device Components
Ergonomic cases, buttons, and interfaces for portable medical technology with precise fit and durability for daily clinical use.
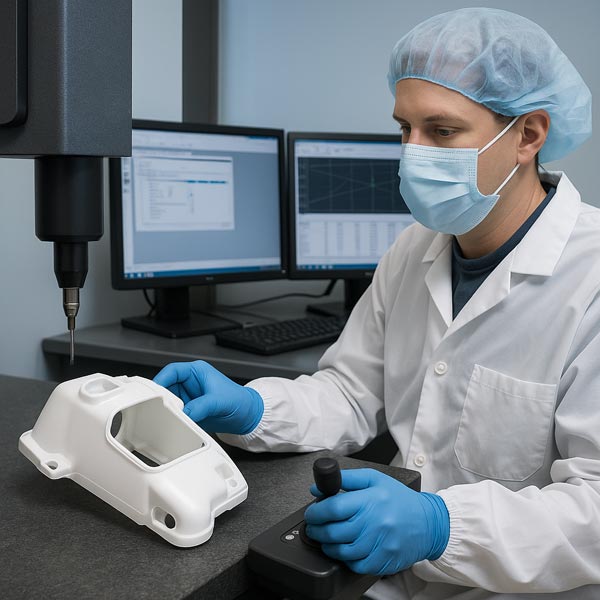
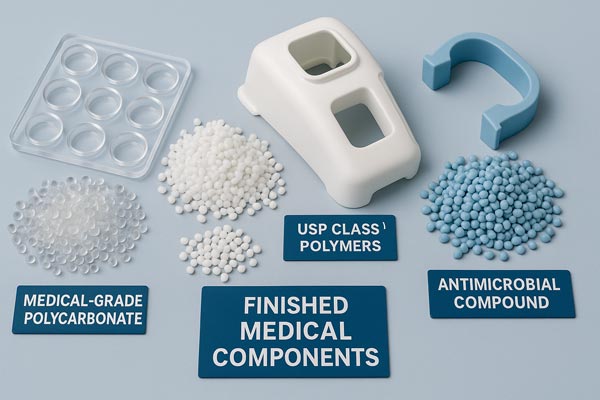
Material Options for Medical-Grade Components
For medical and healthcare applications, we can recommend specialized materials based on their safety, performance, and compliance with industry regulations. We can advise on a comprehensive range of medical-grade polymers that offer the specific properties required for healthcare environments, from biocompatibility to chemical resistance.
All materials used in manufacturing can be fully documented with material certifications, lot traceability, and quality verification data when required by your specifications. This documentation can support your regulatory submissions and provide transparency throughout the production process. We provide comprehensive material guidance based on your application requirements, but customers make all final material selection decisions, particularly for applications with potential liability concerns.
Medical-Grade Materials We Can Work With
- USP Class VI certified medical polymers
- Medical-grade polycarbonate (PC) with exceptional clarity
- Antimicrobial compounds for healthcare environments
- Chemical-resistant materials for laboratory applications
- High-performance acrylics (PMMA) for optical clarity
- Medical-grade ABS for durable structural components
- Thermoplastic elastomers (TPE) for flexible applications
- Material traceability documentation when required
Material Selection Considerations
- Biocompatibility requirements
- Chemical resistance needs
- Sterilization compatibility
- Clarity and optical properties
- Dimensional stability
- Mechanical properties
- Regulatory compliance
- End-use environment
Quality Control for Medical Manufacturing
Precision Measurement & Verification for Healthcare Components
The medical industry requires quality control systems to ensure component reliability and consistency. Our facility includes quality verification technology, such as the Brown and Sharpe CMM (Coordinate Measuring Machine) capable of dimensional verification to ±0.0001 inches. This precision allows us to manufacture medical components to the tight tolerances specified in your designs.
When requested by customers, we can implement Statistical Process Control (SPC) methodologies for medical manufacturing, with in-process monitoring and data collection to verify consistency across production runs. Our quality systems can include monitoring protocols based on your specifications to meet the requirements for your healthcare products.
Documentation is an important component of manufacturing medical components, and we can maintain detailed records for your production batch when specified. This can include material certifications, process parameters, inspection results, and traceability data according to your requirements. Our measurement capabilities allow us to verify that medical components meet the dimensional specifications you provide, with reports available to support your regulatory documentation needs.
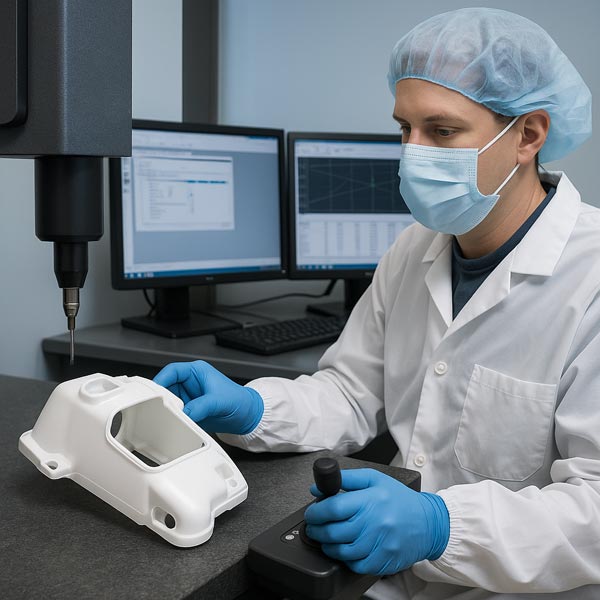
Production Approaches for Medical Plastic Components
Manufacturing components for the medical device industry requires attention to the specific requirements provided by our customers. Our facility can implement the production protocols you specify for your project, adapting our processes to meet your detailed requirements for medical-grade plastic manufacturing.
Production Process Implementation
Our manufacturing environment uses standard protocols for injection molding operations. When your medical plastics applications require specific production parameters, we can implement the procedures you specify. Our team works with you to follow the manufacturing protocols based on your detailed product specifications for your project.
Material Handling According to Requirements
When your specifications call for it, we can implement the material handling procedures you require for your medical plastics. This can include maintaining separation between materials and establishing inventory controls based on your documentation requirements. We follow your guidelines for handling the plastic polymers used in your medical device components.
Production Team Implementation
Our production team follows established procedures and can implement the specific protocols you provide for your medical plastic parts. When you supply detailed requirements for the production of medical-grade plastic components, our team can follow these procedures to maintain consistency with your standards for medical plastics manufacturing.
Verification to Your Requirements
We can implement the verification procedures you specify for your medical devices components. Our measurement equipment can be used to verify the dimensions and characteristics outlined in your specifications. When your medical device manufacturing process requires specific verification points, we can incorporate these into the production flow. If you specify statistical process controls for critical parameters of your project, we can collect and provide this data to support your quality requirements for medical devices.
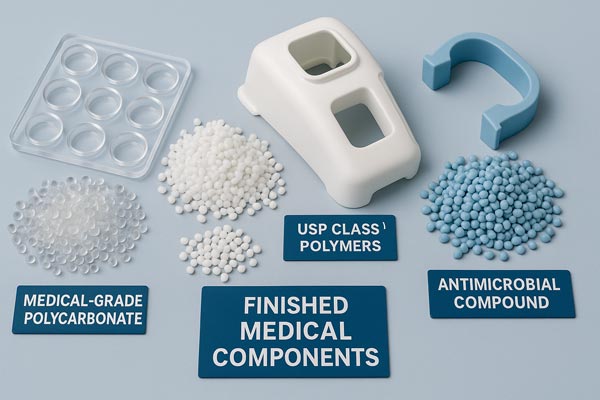
Understanding Medical Plastics & Device Manufacturing
How are medical plastics different from standard industrial plastics?
Medical plastics differ significantly from standard industrial polymers in several important ways. Medical plastics undergo rigorous testing and validation to ensure they meet biocompatibility standards. The manufacturing of medical plastics requires specialized production environments with contamination controls that aren't typically necessary for standard materials. Medical plastics used in healthcare applications often need to withstand repeated sterilization without degradation. When customers select medical plastics for their projects, they typically consider regulatory requirements, performance characteristics, and end-use environment. Many medical plastics are formulated specifically for use in medical devices where they may have direct or indirect patient contact. The production of components from medical plastics generally follows stricter documentation protocols than standard plastic manufacturing. Medical plastics often carry premium pricing due to the additional testing, validation, and quality systems required for their manufacture. While we can process many medical plastics according to your specifications, the selection of appropriate medical plastics for your application remains your responsibility, particularly regarding compliance with standards like ISO 10993.
What should customers know about medical grade plastic components manufacturing?
When manufacturing medical grade plastic components, several key considerations should inform your planning process. Medical plastic components typically require more comprehensive documentation than standard plastic parts. The design should account for their specific end-use environment, including chemical exposure and cleaning procedures. Medical plastic components often undergo more rigorous inspection protocols, with tighter acceptance criteria for dimensional and visual defects. The manufacturing process for medical plastics frequently includes additional in-process verification steps compared to standard production. Material selection should be driven by your regulatory requirements and the specific performance needs of your application. The qualification and validation of medical grade plastic components manufacturing processes are typically more extensive than for non-medical parts. When you partner with Norco, we can implement the specific quality protocols you specify for your medical applications, while you maintain responsibility for regulatory compliance and material selection decisions.
How should manufacturers approach material selection for medical devices?
Material selection for medical devices requires a systematic approach that considers multiple factors. Medical devices often require materials that have been tested according to standards like ISO 10993 or USP Class VI. The mechanical properties of materials used in medical devices must be appropriate for the specific application, considering factors like load requirements and impact resistance. Medical devices may be exposed to various sterilization methods, so materials must be compatible with the intended sterilization processes. Chemical resistance is particularly important for medical devices that may be exposed to cleaning agents, disinfectants, or bodily fluids. When selecting materials for medical devices, manufacturers typically evaluate multiple grades of medical plastics to identify the optimal balance of properties. Regulatory requirements for medical devices vary by device classification and market, influencing material selection decisions. While we can process the materials you specify for your medical devices, the responsibility for material selection and verification of regulatory compliance remains with you as the medical device manufacturer. Our role is to manufacture components to your specifications using the medical plastics you've determined are appropriate for your medical devices.
What quality systems are important for medical plastics manufacturing?
Quality systems for medical plastics manufacturing typically incorporate several specialized elements. Medical plastics production often requires enhanced traceability systems compared to standard plastic manufacturing. Process validation is particularly important for medical plastics to ensure consistent production of conforming parts. In-process monitoring for medical plastics may include additional verification steps at critical stages of production. Statistical process control methodologies are commonly applied to key parameters in medical plastics manufacturing. Material handling protocols for medical plastics typically include measures to prevent cross-contamination between different material types. Documentation systems for medical plastics generally include more detailed records of process parameters and quality checks. While we can implement the quality systems you specify for your medical plastics manufacturing, you determine the appropriate level of quality control based on your regulatory requirements and risk assessment. Our measurement capabilities allow us to verify that components made from medical plastics meet your dimensional specifications, and we can provide the documentation you require to support your quality system.
What documentation is typically required for medical devices components?
Documentation for medical devices components is generally more comprehensive than for standard industrial parts. Medical devices manufacturers typically require material certifications that confirm the identity and grade of plastics used in production. Process validation documentation is often necessary for medical devices to demonstrate that manufacturing processes consistently produce components meeting specifications. First article inspection reports for medical devices components usually include detailed dimensional verification against all specified requirements. Batch records for medical devices components frequently include processing parameters, inspection results, and traceability information. Medical devices manufacturers may require non-conformance documentation that details any deviations and their disposition. Change control documentation is particularly important for medical devices, as changes to materials or processes may require revalidation. While we can provide the documentation you specify to support your medical devices manufacturing, you determine the documentation requirements based on your regulatory needs. Our documentation capabilities are designed to support your quality system for medical devices while you maintain responsibility for regulatory compliance.
Need Precision Medical Components with Complete Traceability?
Contact us about your medical or healthcare application. Our facility specializes in precision manufacturing for non-invasive medical components with the quality control systems and documentation that medical device manufacturers require. From diagnostic equipment components to laboratory sample containers, we deliver exceptional quality with complete traceability and consistent performance across production runs.
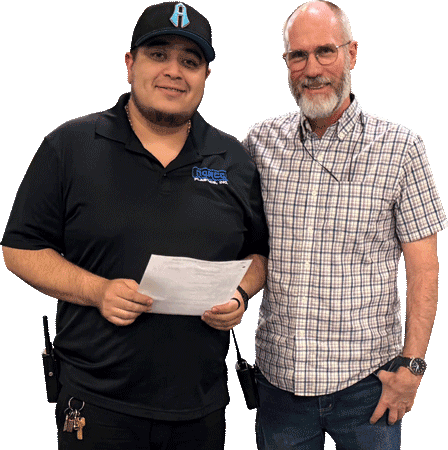