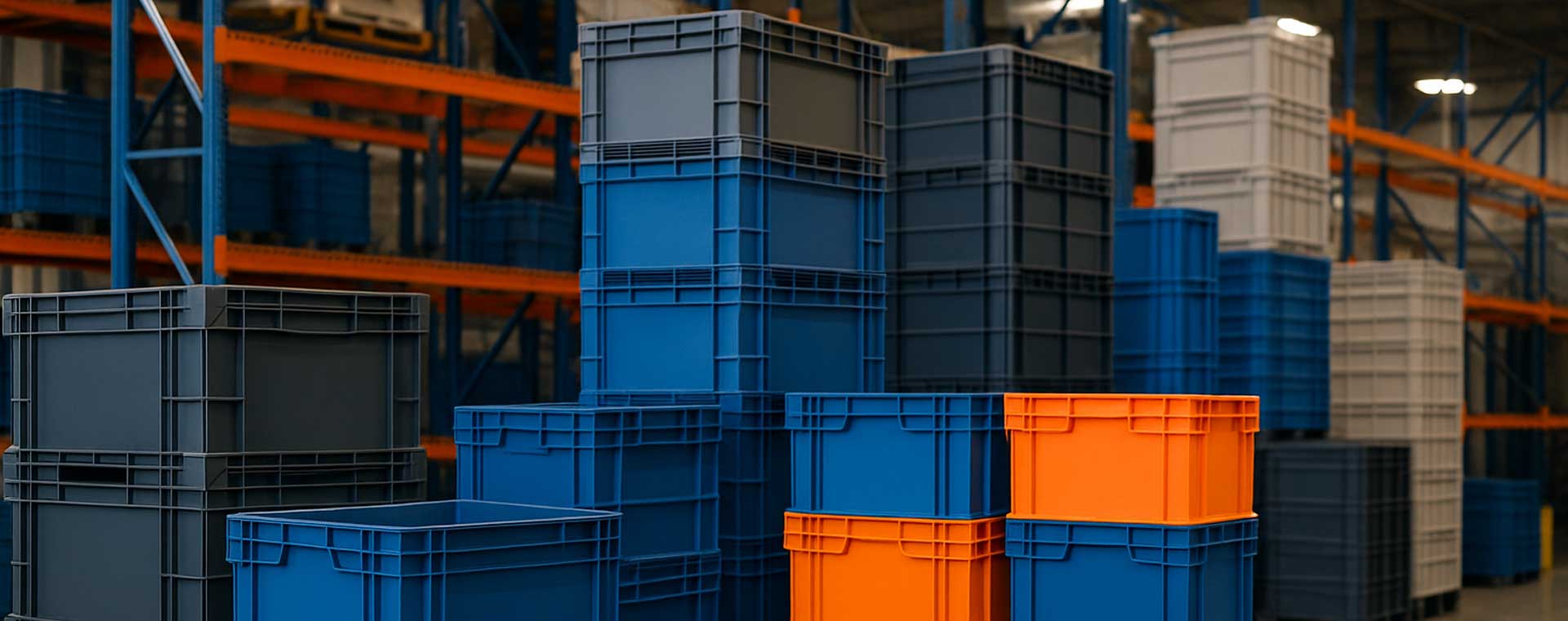
Storage & Distribution Plastic Component Manufacturing
Our Southern California facility offers comprehensive distribution tray manufacturing capabilities spanning from 30 to 2800 ton of clamp force, enabling production of everything from small beverage tray production runs to large industrial plastic totes manufacturing. For clients in the food industry, we provide consultation on food storage container manufacturing options that align with FDA compliance requirements. With over 50 years of manufacturing expertise, we collaborate with storage and distribution professionals to develop solutions that improve operational efficiency and reduce costs through customized designs that meet specific workflow and environmental requirements.
Impact-Resistant
REINFORCED DESIGNS
FOR DISTRIBUTION ENVIRONMENTS
Space-Optimized
STACKABLE CONTAINERS
FOR EFFICIENT LOGISTICS
Customized Solutions
TAILORED DESIGNS
FOR OPERATIONAL EFFICIENCY
Meeting the Demanding Requirements of Logistics Operations
The storage and distribution industry faces unique challenges that require specialized plastic components designed for durability, efficiency, and consistency. From impact resistance to dimensional precision, Norco's manufacturing capabilities address the critical requirements of modern logistics operations. Our collaborative approach helps clients overcome common challenges while optimizing their distribution workflows.
Impact Resistance Requirements
Distribution environments subject containers to frequent impacts during handling, stacking, and transportation. Our approach includes recommending high-impact polymer options and reinforced designs for critical stress points. We help clients evaluate different materials based on their specific durability requirements and operational conditions.
Space Optimization & Stackability
Warehouse and transportation efficiency demands maximizing usable space while ensuring safe stacking. Our team works with clients to develop interlocking designs, reinforced corners, and load-bearing structures that optimize vertical space utilization without compromising stability or safety during loading, transport, and storage.
Dimensional Consistency for Automation
Modern logistics systems rely on precise dimensions for automated handling equipment. Our manufacturing processes maintain tight tolerances critical for conveyor systems, robotic handling, and automated storage/retrieval systems. We work with clients to ensure components align with their specific automation requirements.
Cost-Effectiveness for High Volume
High-volume distribution requires balancing quality with cost-efficiency. Our tooling and production capabilities are designed for optimal efficiency with minimal material waste. We collaborate with clients to identify cost-reduction opportunities through design optimization, material selection guidance, and efficient production scheduling.
Weight Efficiency Considerations
Transportation costs and payload limitations make weight optimization crucial. We advise on lightweight polymer options that balance durability with weight efficiency, using strategic reinforcement only where structurally necessary. This approach helps clients reduce shipping costs while maintaining required strength and performance characteristics.
Our Collaborative Approach
At Norco Plastics, we understand that each storage and distribution operation faces unique challenges. Our approach focuses on working collaboratively with clients to understand their specific requirements before providing tailored recommendations that address their particular pain points while optimizing operational efficiency.
Storage & Distribution Applications
Manufacturing Capabilities for Client-Designed Components
Our manufacturing capabilities extend across a wide range of storage and distribution applications. We partner with clients to manufacture their custom-designed components according to their specifications for improved operational efficiency and industry-specific requirements.
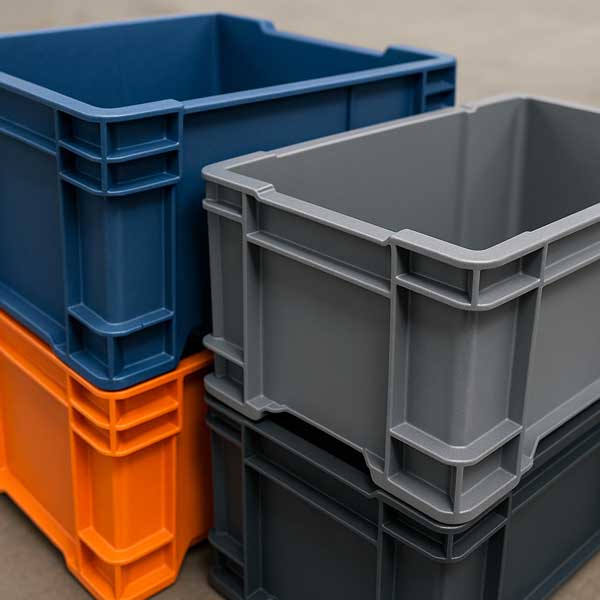
Storage Totes with Reinforced Corners
We manufacture storage containers according to client designs, including those requiring reinforced corners for impact resistance and stackability. Our manufacturing capabilities can produce totes with various wall thicknesses and in multiple sizes based on your operational specifications.
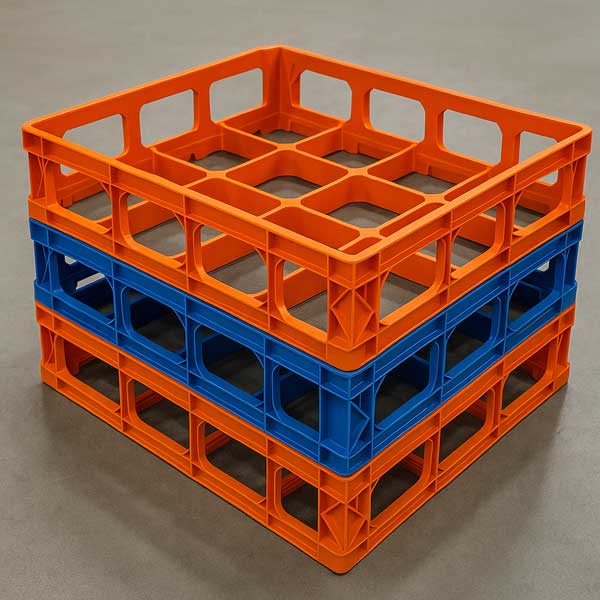
Bakery and Beverage Trays
We can manufacture food-grade trays for bakery and beverage applications according to your designs. Our capabilities include working with FDA-compliant materials and producing trays with stacking features based on your specific requirements for product protection and transportation.
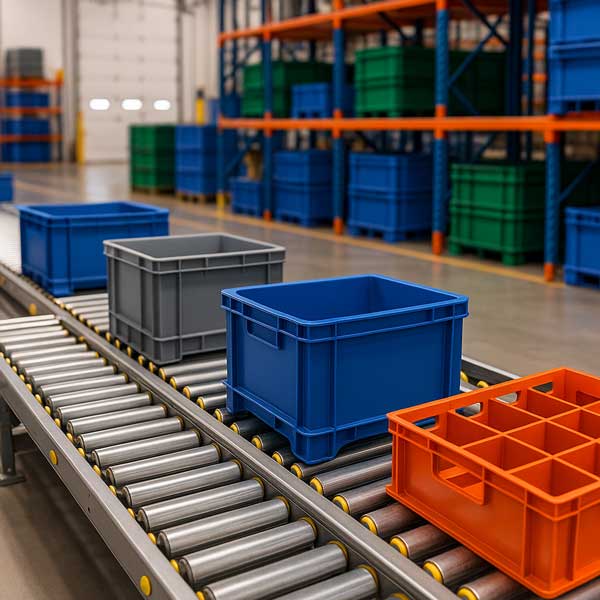
Logistics Transport Trays
We manufacture custom logistics trays according to your design specifications. Our precision manufacturing capabilities can produce trays with consistent dimensions for automated handling systems, nesting features, and durable construction for challenging distribution environments.
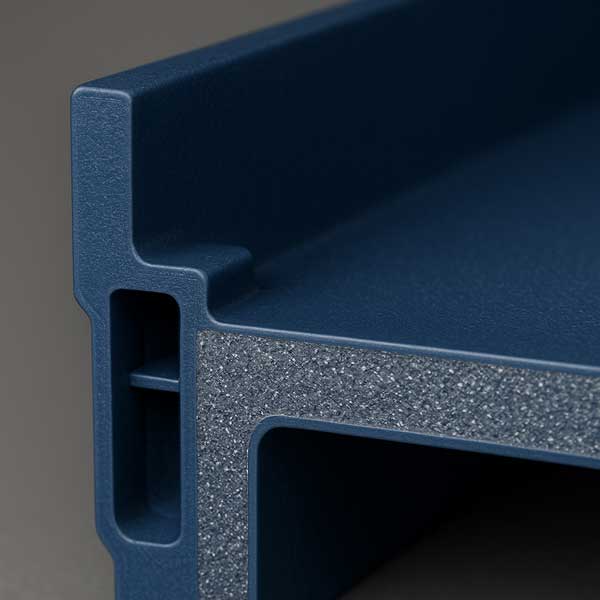
Food Storage Solutions
We can manufacture FDA-compliant containers according to your designs for food preservation and distribution. Our capabilities include working with specialized materials for temperature resistance and chemical stability to meet your requirements for product integrity throughout the supply chain.
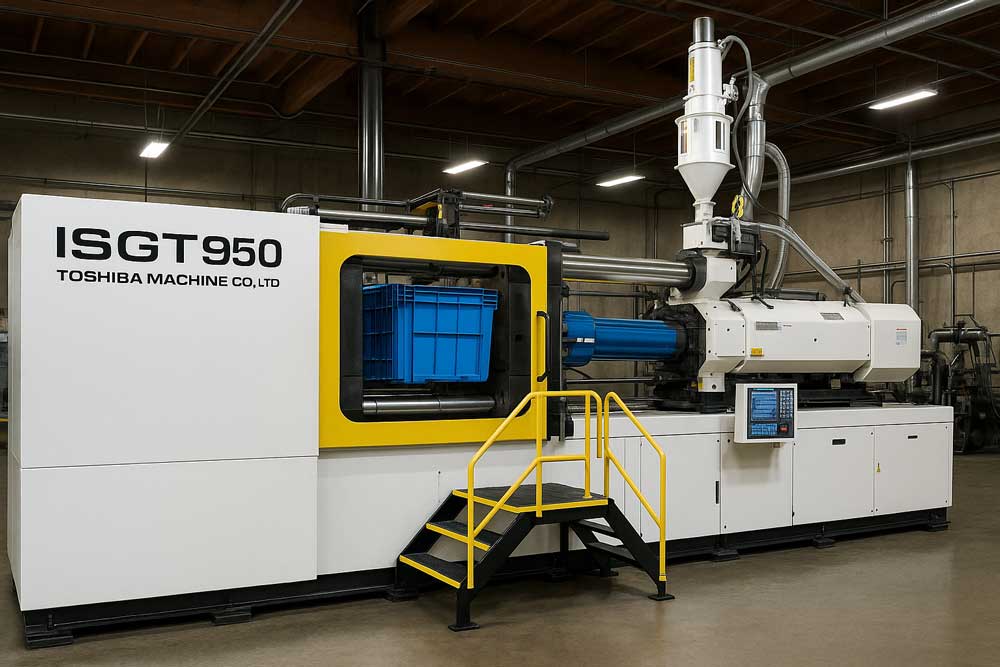
Stackable Container Systems
We manufacture components for integrated storage systems designed to your specifications. Our precision manufacturing capabilities can produce interlocking mechanisms and reinforced load-bearing areas according to your design for warehouse efficiency and structural integrity.
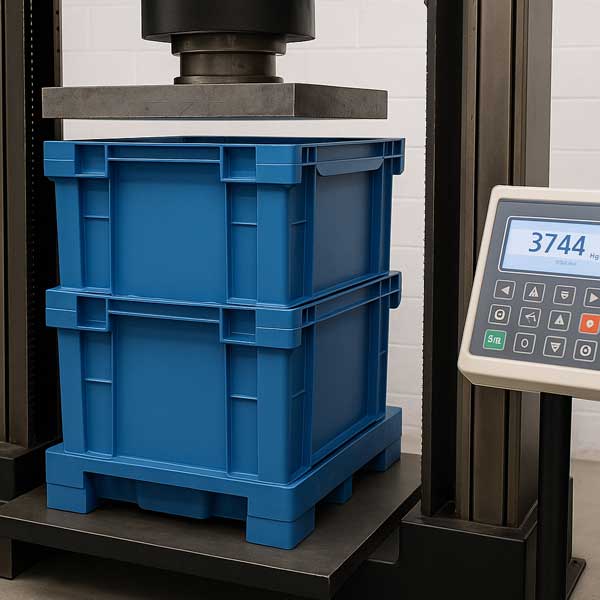
Warehouse Storage Solutions
We can manufacture specialized components for warehouse organization per your design specifications. Our manufacturing capabilities support the production of bins, dividers, and organizational systems designed to your requirements for space utilization and inventory management.
Need a custom storage or distribution solution for your specific operational needs?
Request a Storage Component ConsultationMaterials for Storage Applications
For storage and distribution applications, material selection plays a critical role in product performance. We provide guidance on a range of specialized polymers and compounds that deliver the specific characteristics required for demanding logistics environments. Our team works with clients to evaluate material options based on their unique operational requirements.
High-Impact Polymers
Engineered materials featuring exceptional impact strength for applications subject to frequent handling, stacking, and transportation. These polymers provide superior resistance to cracking, breaking, and deformation under load.
Reinforced Compounds for Load-Bearing
Composite materials enhanced with reinforcing agents that significantly improve structural strength and rigidity. These compounds are ideal for applications requiring high load-bearing capacity while maintaining dimensional stability.
Food-Grade Materials for Consumable Storage
FDA-compliant polymers formulated specifically for direct food contact applications. These materials meet strict regulatory requirements for chemical composition and leaching, ensuring safety throughout the food supply chain.
Lightweight Yet Durable Formulations
Advanced polymer blends optimized for the ideal balance of weight and strength. These materials help reduce shipping costs and improve handling ergonomics while maintaining essential durability requirements for distribution operations.
Material Selection Considerations
Our approach to material selection involves thorough consultation with clients to understand their specific operational requirements. Factors we consider include impact resistance needs, load-bearing requirements, environmental exposure conditions, temperature ranges during use, chemical compatibility, and regulatory compliance needs. We provide guidance on material options that address these factors while optimizing cost-effectiveness for your specific application.
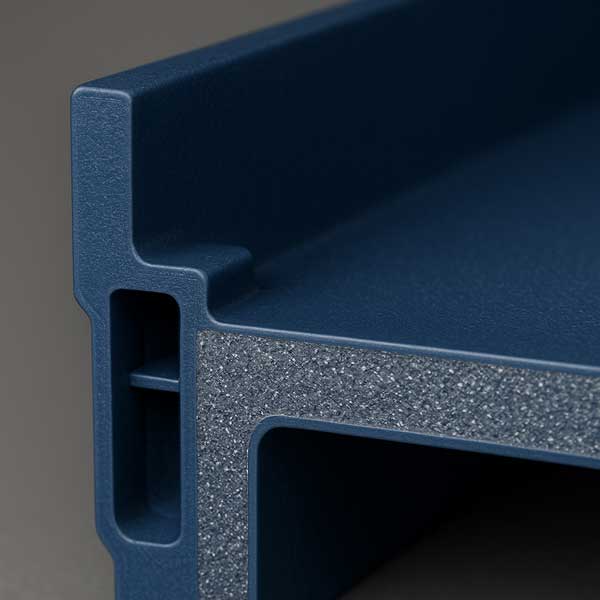
Performance Characteristics Under Load and Impact
- ✓ Superior crack resistance under repeated impact
- ✓ Maintained dimensional stability under sustained load
- ✓ Excellent stress distribution for corner and edge protection
- ✓ Consistent performance across temperature variations
- ✓ UV-resistant formulations for outdoor applications
- ✓ Chemical resistance for cleaning and sanitization processes
Manufacturing Capabilities for Storage Products
Our comprehensive manufacturing facilities are equipped with advanced technology specifically configured for storage and distribution component production. From small precision parts to large structural elements, our range of injection molding machines provides exceptional flexibility and quality for diverse storage applications.
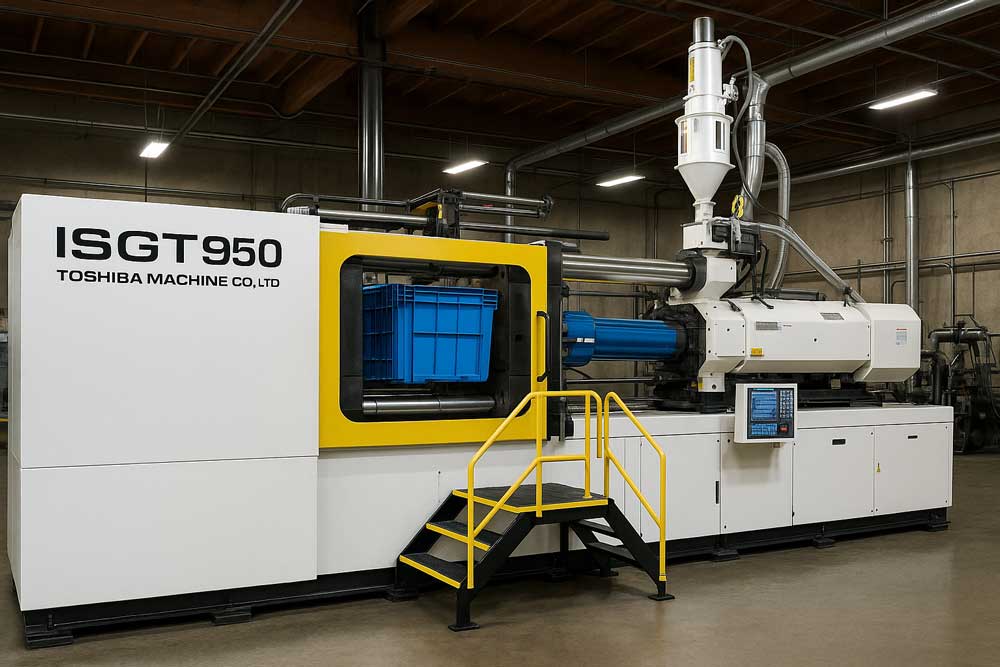
Extensive Production Range
Our facility features injection molding machines ranging from 30 to 2800 ton clamping force, enabling production of components from small organizational dividers to large-scale storage containers. This breadth of manufacturing capability allows us to recommend the most efficient production approach for any storage component.
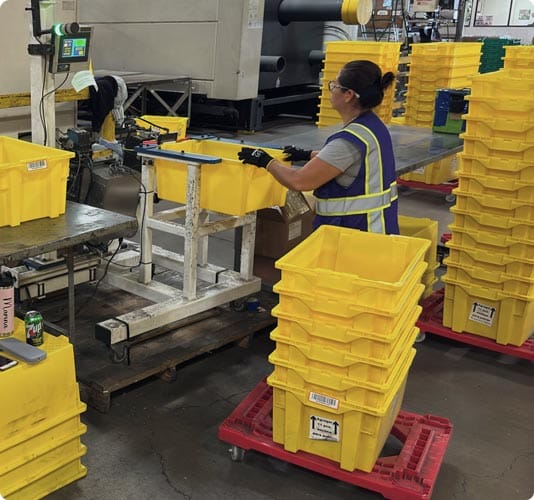
Volume Production Efficiency
Our 24/7 manufacturing capabilities and automated systems are optimized for high-volume production runs typical in storage and distribution applications. Advanced process controls ensure consistent quality while maximizing production efficiency to meet demanding delivery schedules.
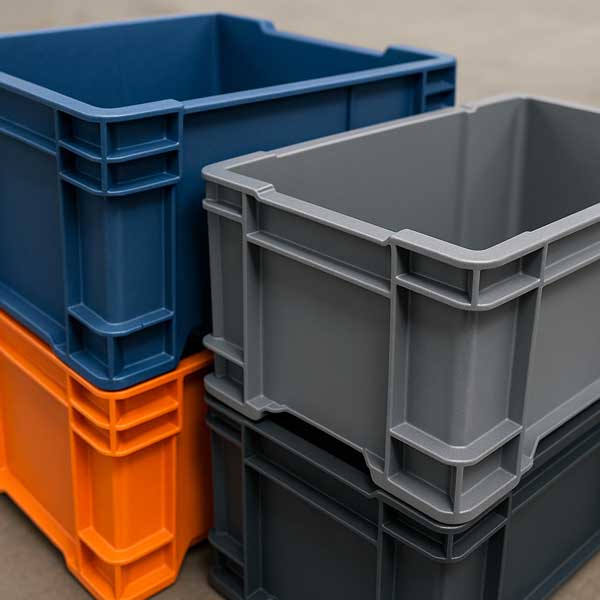
Technical Precision for Storage Applications
Our Brown & Sharpe CMM technology provides measurement precision to ±0.0001 inches, ensuring critical dimensional consistency required for stackable containers and automated handling systems. This technical precision delivers components that meet exact specifications for optimal operational performance.
Statistical Process Control
Advanced monitoring systems that continuously track critical parameters throughout production, ensuring consistent quality across high-volume runs while immediately identifying potential variations.
Efficient Production Cycles
Optimized cycle times through advanced temperature control, cooling system design, and material pre-conditioning that maintains quality while maximizing production throughput for cost-effective manufacturing.
First Article Inspection
Comprehensive validation process that verifies the first production parts against all specifications before full production runs begin, ensuring complete compliance with design requirements.
Material Handling Systems
Automated material delivery and preparation systems that ensure optimal material condition prior to molding, reducing variation and improving consistency in final component properties.
Storage Component Manufacturing Capabilities
Storage Tote Manufacturing
- Manufacturing sizes: 12" x 8" to 48" x 32"
- Wall thickness capabilities: 0.125" to 0.250"
- Can manufacture designs up to 200 lbs capacity
Stackable Component Production
- Manufacturing for stacking designs
- Interlocking feature precision: ±0.005"
- Materials suitable for -40°F to 180°F
Food-Grade Manufacturing
- FDA-Compliant Materials available
- Temperature range capabilities: -20°F to 250°F
- USDA-approved colors available
Logistics Tray Production
- Manufacturing precision: ±0.010"
- Can produce nesting designs for space efficiency
- Suitable for automation-compatible designs
Performance Standards & Testing
Our manufacturing processes include quality control protocols to ensure components meet performance standards. We offer various testing procedures upon client request to verify component integrity under specific conditions.
Load Testing & Stacking Strength
Upon client request, we can perform load testing to verify stacking strength under specific conditions. Tests can include static load capacity, dynamic load in motion, and long-term creep under sustained pressure as specified by the client. Components can be evaluated at specific temperature ranges to validate performance in various operational environments when required.
Impact Resistance Testing
When specified by the client, we can subject components to impact testing to evaluate durability during handling and transportation. Available testing procedures include drop tests, corner impact testing, and repeated impact evaluation to simulate specific conditions. These tests can help predict component performance in supply chain environments based on client requirements.
Dimensional Consistency Measures
Our Brown & Sharpe CMM technology provides measurement precision to ±0.0001 inches, allowing us to verify critical dimensional consistency for components. We use statistical process control methods to monitor production and ensure dimensions remain within client-specified tolerances, supporting reliable performance in automated systems where required.
Material Safety for Food Contact
For food-grade container manufacturing, we can provide guidance on FDA-compliant materials. Upon client request, we can arrange for specialized testing including leaching tests and material certification documentation to support regulatory compliance. We can also manufacture products suitable for applications requiring specific temperature resistance for hot-fill or refrigeration.
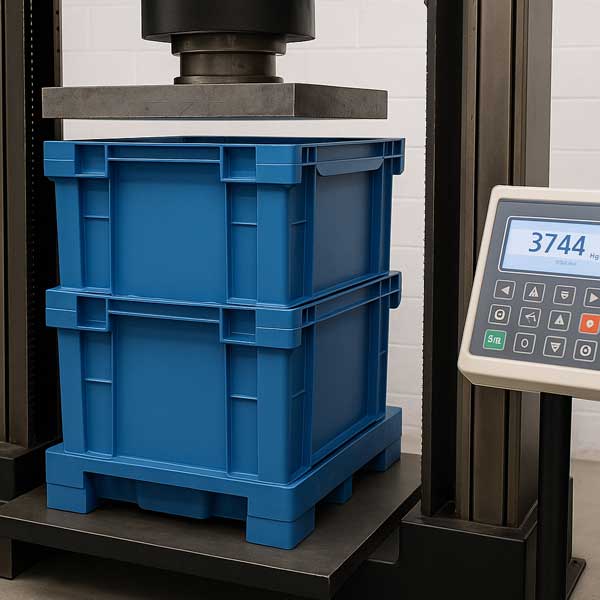
Quality Assurance Documentation
We can provide quality documentation packages based on client specifications. Available documentation types include verification reports for performance characteristics specific to your application, which can support your internal quality requirements and provide reference data for production.
- First Article Inspection Reports
- Material Certification Reports
- Statistical Process Control Reports
- Performance Test Results (when requested)
Common Questions About Storage & Distribution Components
What types of storage containers can Norco manufacture?
Norco Plastics manufactures a diverse range of storage containers and distribution components including reinforced storage totes with sizes ranging from 12" x 8" to 48" x 32", stackable container systems with interlocking features, food-grade containers compliant with FDA regulations, logistics and transport trays with automation-compatible designs, beverage and bakery trays for food distribution, and customized storage solutions for specific industry requirements. Our large tonnage capabilities (up to 2800 ton) allow us to produce containers of substantial size that many manufacturers cannot accommodate. We work with clients to understand their operational requirements and recommend appropriate designs and materials for their specific application.
What design considerations are important for stackable components?
When manufacturing stackable components, several design considerations are important for optimal performance. These include incorporating reinforced corners and load-distributing ribs in the design for structural integrity, using materials that provide adequate structural rigidity and compression resistance for stacking applications, ensuring precise interlocking features are manufactured to tight tolerances (typically ±0.005") for consistent and secure stacking, and designing for the expected temperature range of operation. Our manufacturing expertise can help bring your stackable container designs to life with precision and quality that ensures reliable performance in warehouse and distribution environments.
What material options provide the best impact resistance?
Several material options can provide excellent impact resistance for storage and distribution applications. We help clients evaluate options including High-Impact Polypropylene (HIPP) which provides excellent impact resistance across a wide temperature range, making it ideal for containers subject to varied environmental conditions; ABS (Acrylonitrile Butadiene Styrene) which offers good impact strength with excellent surface finish, suited for applications that require both durability and aesthetic appeal; Polycarbonate Blends which provide exceptional impact resistance in transparent or opaque applications where visibility may be required; Glass-Fiber Reinforced Polymers which add structural rigidity and impact resistance for heavy-duty applications; and HDPE with Impact Modifiers as a cost-effective solution with improved impact performance for many general storage applications. The optimal material choice depends on the specific application requirements including temperature range, chemical exposure, UV exposure, and cost considerations. We work with clients to understand these factors and provide guidance on appropriate material options for their particular application.
Can Norco produce food-grade storage containers?
Yes, we manufacture food-grade storage containers and components using FDA-compliant materials and processes. Our food-grade container manufacturing includes FDA-Compliant Materials that comply with FDA regulations for direct food contact (21 CFR 177.1520 for polyolefins and other applicable standards), temperature range considerations for containers that withstand temperatures from -20°F to 250°F (accommodating freezing, refrigeration, and hot-fill applications), USDA-Approved Colorants when color is required, proper manufacturing processes to prevent contamination during production, and comprehensive documentation to support regulatory compliance requirements. Our food-grade containers are suitable for bakery products, produce, prepared foods, ingredients, and other food industry applications. We work with clients to understand their specific food storage requirements including cleaning protocols, temperature conditions, and handling processes to provide appropriate container solutions.
What is the largest storage container size Norco can manufacture?
With our large tonnage injection molding capabilities of up to 2800 ton, we can manufacture substantial storage containers and components. Our equipment can handle up to 1000 oz of material per shot, allowing for large-volume components. For pallet-sized items, we can produce components up to approximately 48" x 48" x 4", though this is at the upper limit of our capabilities due to weight considerations. For applications requiring larger storage solutions, we can manufacture multi-component systems that assemble into larger containers. Maximum wall thickness can range from 0.125" to 0.5" depending on material requirements and design specifications. For specific large container requirements, our engineering team can evaluate your application and provide guidance on feasibility, design approach, and material selection to achieve the required size while maintaining necessary performance characteristics.
Need Custom Storage & Distribution Solutions for Your Operation?
Contact us about your next storage or distribution project. Our facility features advanced injection molding equipment with capabilities ranging from 30 to 2800 ton for manufacturing precision storage components. We work collaboratively with clients to optimize designs for durability, stackability, and operational efficiency. Our experienced team delivers reliable storage solutions with 24/7 manufacturing capabilities and comprehensive quality control systems.
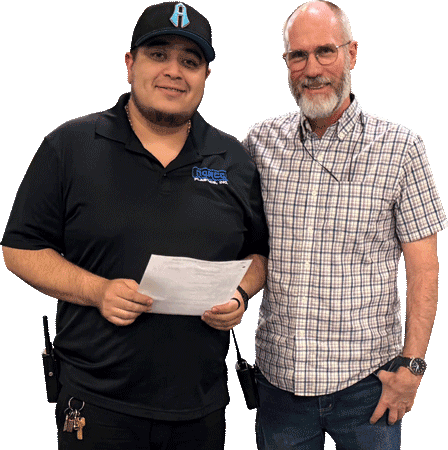