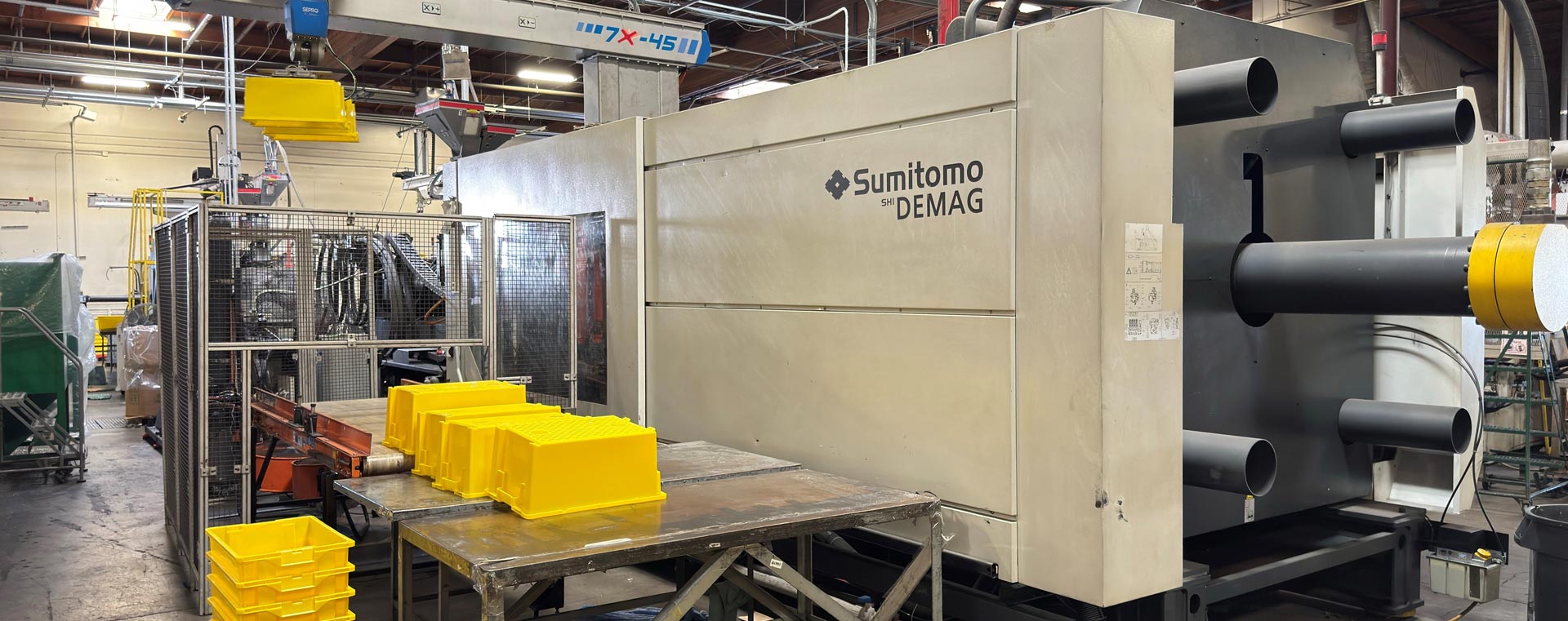
Turnkey Manufacturing Solutions & Specialty Injection Molding Services
Our full-service injection molding approach includes specialized injection molding services such as structural foam molding, insert molding, and multi-material techniques that address unique application requirements. By managing the entire manufacturing process from design to delivery, we eliminate communication barriers, reduce lead times, and ensure consistent quality throughout production. Our Southern California facility provides complete manufacturing solutions for clients throughout Los Angeles, Orange County, Riverside, and San Diego.
50+ Years
TURNKEY MANUFACTURING
EXPERIENCE
40%
LEAD TIME REDUCTION
WITH INTEGRATED SERVICES
Complete
PROJECT MANAGEMENT
FROM CONCEPT TO DELIVERY
From Concept to Completion
Our comprehensive end-to-end manufacturing process ensures a seamless journey from initial concept to finished product. By managing every stage of production under one roof, we eliminate communication barriers, reduce lead times, and maintain consistent quality throughout. Our systematic approach allows us to optimize each phase of the manufacturing process while providing complete transparency and regular updates throughout your project.
Design Assistance & Optimization
Our engineering team provides DFM (Design for Manufacturing) guidance and material recommendations to optimize your part designs for manufacturability, performance, and cost-efficiency. We can guide you to qualified design partners for 3D modeling and detailed design services to refine your concept before tooling begins.
Material Selection & Tooling Development
We guide material selection based on your application requirements, budget, and performance needs. We work with trusted third-party tooling partners to develop precision molds, and verify critical aspects such as cooling, gating, and ejection systems to ensure consistent quality across high-volume production runs.
Production Planning & Manufacturing
Our production team develops detailed manufacturing plans including cycle times, machine setup, and quality control measures. Using our advanced injection molding equipment, we produce components with precision while monitoring critical parameters throughout the production process.
Quality Control & Documentation
We provide quality control services tailored to your specific requirements, including first article inspection reports and targeted dimensional verification. Our quality procedures can be customized to focus on the specific measurements and tests that are most important for your application and compliance needs.
Assembly & Secondary Operations
Our assembly services integrate multiple components into finished products using automated and manual techniques. We offer secondary operations including hot stamping, pad printing, and decorative finishing to enhance functionality and visual appeal of your products.
Packaging & Logistics
We develop custom packaging solutions that protect your products during shipping and storage. Our just-in-time delivery system, inventory management, and Southern California distribution network ensure your products arrive on schedule to any location throughout the region.
Advanced Molding Techniques for Specialized Applications
Our end-to-end manufacturing solutions include specialized injection molding techniques that address unique application requirements. Beyond conventional injection molding, we offer advanced manufacturing processes that provide enhanced performance characteristics, complex geometries, and specialized material combinations that standard molding cannot achieve.
Our structural foam molding capability creates lightweight yet exceptionally strong plastic parts with solid outer surfaces and cellular cores. This process is ideal for large components requiring high strength-to-weight ratios and superior structural rigidity. Our high-pressure injection molding machines with specialized foaming agents deliver consistent quality across complex geometries and challenging design requirements.
For multi-material applications, our insert molding and overmolding processes combine different materials in a single component. These techniques allow for the integration of metal inserts, electronic components, or different plastic materials to create complex assemblies with enhanced functionality. Our specialized material processing expertise includes working with reinforced materials, high-temperature polymers, and specialty compounds designed for specific performance requirements.
Advanced Molding Techniques Available
- Structural foam molding for lightweight, strong components
- Insert molding for metal-to-plastic integration
- Overmolding for multi-material components
- Specialized material processing for unique requirements
- Large part manufacturing with up to 2800 ton capacity
- Thin-wall molding for lightweight, high-precision parts
Common Specialty Molding Applications
- Large structural components
- Multi-material assemblies
- Metal-plastic hybrid parts
- Reinforced composite components
- Chemical-resistant containers
- High-temperature applications
- Impact-resistant housings
- Complex automotive assemblies
Project Management Approach
Dedicated Team Management for Complex Manufacturing Projects
Our turnkey manufacturing solutions include a comprehensive project management approach that ensures clear communication, efficient workflows, and timely delivery. Each project is assigned a dedicated project manager who serves as your single point of contact throughout the manufacturing process, from initial design to final delivery.
We implement structured communication protocols including regular status updates, milestone reviews, and collaborative problem-solving sessions to keep your project on track. Our project management team develops detailed timelines with critical path analysis, establishes quality checkpoints throughout the process, and creates comprehensive documentation to ensure transparency and accountability at every stage.
Our client collaboration methods include secure online platforms for file sharing, video conferences for design reviews, and on-site meetings for critical production phases. This multi-faceted approach ensures that your project requirements are clearly understood, challenges are quickly addressed, and your manufacturing goals are achieved with optimal efficiency and quality.
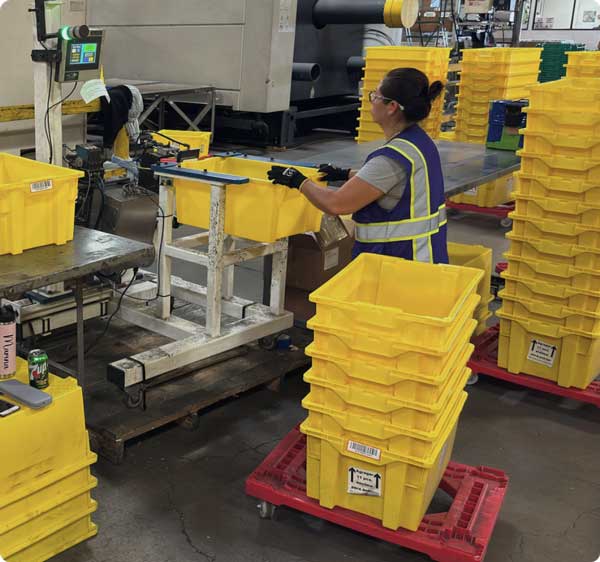
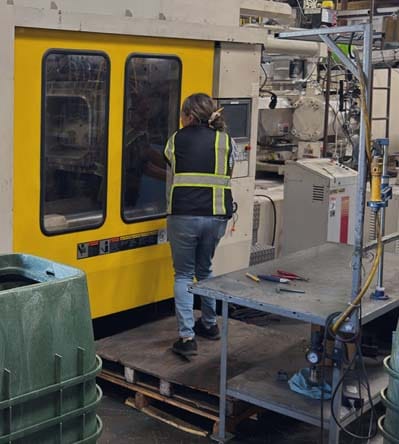
Advantages of End-to-End Manufacturing Solutions
Choosing end-to-end manufacturing solutions with Norco Plastics delivers significant advantages throughout your product development and production processes. By consolidating design, tooling, manufacturing, assembly, and logistics with a single vendor, you eliminate communication barriers that can occur between multiple suppliers. This streamlined approach results in reduced lead times, more efficient production planning, and faster time-to-market for your products.
Our integrated approach ensures consistent quality control throughout the manufacturing process, with standardized procedures and continuous monitoring from initial design through final delivery. This eliminates quality variations that can occur when transitioning between different vendors. By optimizing each phase of production and eliminating redundant processes, our turnkey manufacturing solutions typically reduce overall costs by 15-25% compared to managing multiple separate vendors.
Simplified Vendor Management
Single point of contact for all manufacturing needs, eliminating multiple vendor coordination and communication challenges.
Consistent Quality Control
Standardized quality procedures across all manufacturing phases ensure consistent quality from concept to completion.
Reduced Lead Times
Streamlined transitions between manufacturing phases eliminate delays and reduce overall project timeline by up to 40%.
Cost Efficiencies
Integrated processes eliminate redundancies, reduce logistics costs, and optimize material usage for 15-25% overall cost savings.
Turnkey Manufacturing Solutions for Multiple Industries
Our end-to-end manufacturing solutions serve diverse industries with complex components and multi-part assemblies. We customize our turnkey manufacturing approach to address the unique requirements, standards, and performance expectations for each industry while maintaining consistent quality and efficient production.
Automotive Components
Our turnkey automotive manufacturing solutions include advanced interior and exterior components that meet demanding industry standards. We produce complex multi-material assemblies, structural components requiring precise tolerances, and high-appearance parts with integrated functions. Our end-to-end production ensures quality control throughout the manufacturing process, from material selection through final assembly and testing.
Non-Invasive Medical Solutions
Our non-invasive medical manufacturing capabilities combine medical-grade materials, cleanroom assembly processes when required, and comprehensive documentation for full traceability. We specialize in storage trays, transport containers, and external device housings for the healthcare industry. Our end-to-end approach ensures regulatory compliance throughout the manufacturing process while maintaining the cleanliness and consistency required for healthcare applications.
Consumer Products
Our consumer product manufacturing solutions combine aesthetic design, durability, and cost efficiency. We produce high-quality consumer goods with consistent finishes, precise assembly, and efficient packaging for retail environments. Our turnkey approach integrates branding elements, assembly, and packaging to deliver market-ready products that meet consumer expectations for quality and performance.
Infrastructure Components
Our infrastructure manufacturing solutions focus on durability, structural integrity, and environmental resistance. Using our large tonnage capabilities, we produce substantial components that withstand demanding conditions. Our end-to-end approach ensures consistency across large production volumes while maintaining the critical performance characteristics required for infrastructure applications.
Frequently Asked Questions About End-to-End Manufacturing Solutions
Get answers to common questions about our turnkey manufacturing and specialty molding services. If you need additional information, our team is ready to assist with your specific requirements.
What is included in turnkey manufacturing services?
Our turnkey manufacturing services include every aspect of the production process from initial design assistance through final delivery. This comprehensive approach typically includes design optimization, material selection, tooling design and development, production planning, manufacturing, quality control, assembly and secondary operations, packaging, and logistics. Each project is customized to include the specific services needed for your application, all managed by a dedicated project manager who serves as your single point of contact.
How does Norco handle intellectual property in design collaboration?
We respect the confidentiality and ownership of your intellectual property throughout the design collaboration process. At the beginning of each project, we establish clear agreements regarding IP ownership, confidentiality requirements, and permitted uses of design information. All design files, 3D models, and technical specifications remain your property, and our design assistance is focused on manufacturability improvements rather than fundamental design changes. Our team adheres to strict data security protocols to protect your proprietary information.
What specialized molding techniques does Norco offer?
We offer several specialized molding techniques beyond conventional injection molding, including structural foam molding, insert molding, overmolding, and specialized material processing. Our structural foam capability creates lightweight parts with exceptional strength by producing cellular cores with solid outer surfaces. Insert molding and overmolding allow for the integration of different materials or components in a single part, though our overmolding requires two separate molds and machines. We also have large tonnage capabilities up to 2800 tons for substantial components and specialized material processing expertise for engineering-grade polymers.
How are complex projects managed from start to finish?
Complex projects are managed through our structured project management approach. Each project is assigned a dedicated project manager who serves as your primary contact and coordinator throughout the process. We implement detailed planning with critical path analysis, regular status updates, milestone reviews, and quality checkpoints at key stages. Our project management system provides comprehensive documentation, scheduled progress reviews, and collaborative problem-solving methods. This systematic approach ensures clear communication, maintains timeline adherence, and delivers consistent quality across all project phases.
What are the advantages of using one vendor for the entire manufacturing process?
Using a single vendor for the entire manufacturing process offers several significant advantages. First, it simplifies vendor management with a single point of contact rather than coordinating multiple suppliers. This approach ensures consistent quality control throughout the process with standardized procedures from design through delivery. Integrated manufacturing typically reduces lead times by 30-40% by eliminating transition delays between different vendors. Cost efficiencies are achieved through optimized processes, reduced logistics, and elimination of redundant operations. Additionally, a single vendor provides more effective problem-solving capabilities, enhanced communication, and greater accountability throughout the project.
Need more information about our end-to-end manufacturing solutions?
Contact Our Manufacturing TeamReady to Streamline Your Manufacturing with End-to-End Solutions?
Contact us to discuss your next manufacturing project. Our turnkey solutions combine design assistance, material selection, tooling, production, assembly, and logistics into a seamless process that reduces lead times and ensures consistent quality. Whether you need specialized molding techniques or complete project management, our team can develop a customized manufacturing solution for your specific requirements.
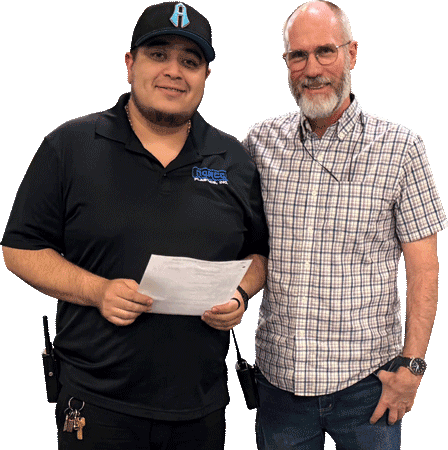