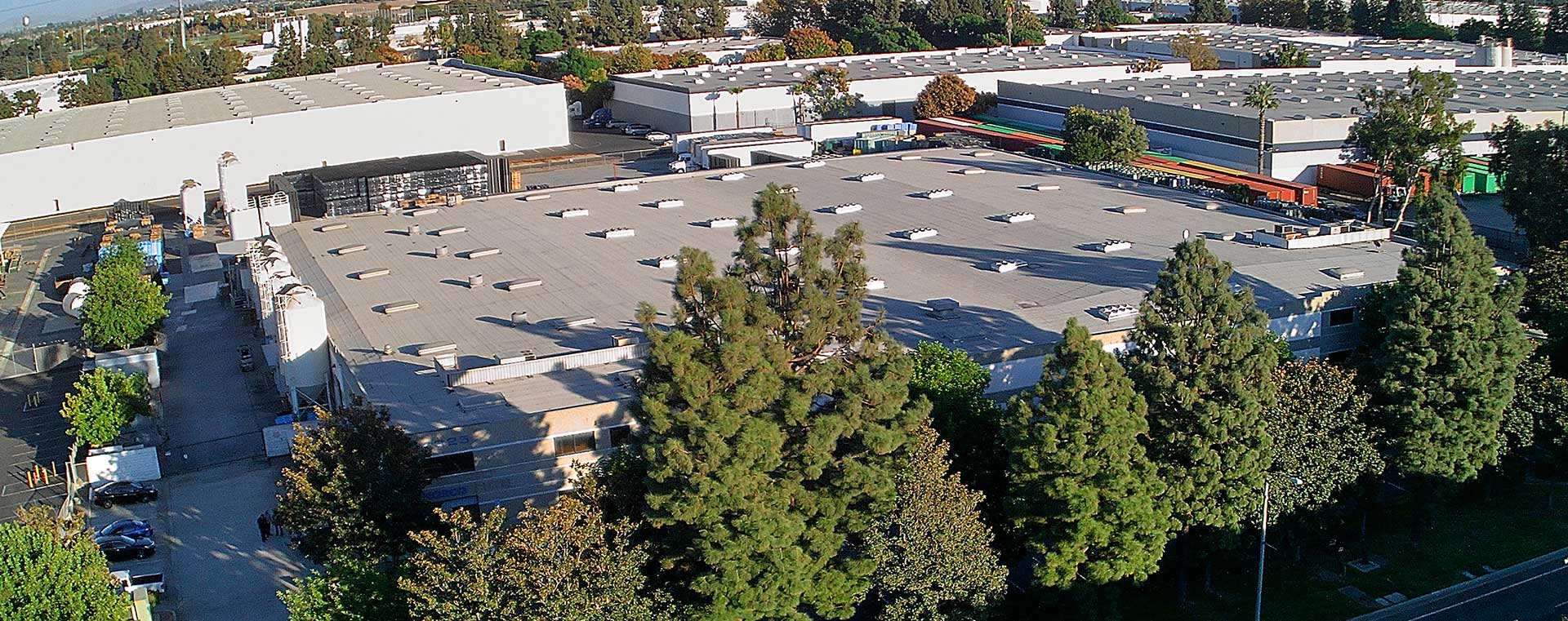
Custom Plastic Injection Molding Quotes
Get accurate pricing for your plastic injection molding quote from one of Southern California's leading custom plastic molding companies
Request Your Plastic Injection Molding Quote
Custom Injection Molding Services & Quotes
What information should I prepare for my plastic injection molding quote request?
When requesting an injection molding quote, providing comprehensive details helps us deliver accurate pricing and production timelines. The most essential information includes your 3D CAD files (preferably in STEP, IGES, or native SolidWorks format) so we can analyze part geometry, wall thickness, and complexity. Clearly specify your material requirements - whether standard thermoplastics or engineering plastics with specific chemical resistance properties. Include your target production volume, as the mold tooling costs are distributed differently across various quantities. Define any surface finish requirements, color specifications, and secondary operations such as assembly or decorating. For parts with critical dimensions, highlight which tolerances are most important. Our injection molding service specializes in transforming these specifications into precise, manufacturable parts. The more detailed information you provide, the more accurate your quote will be and the better we can optimize the manufacturing process for your specific needs.
What industries commonly use injection molded parts in their products?
Injection molding is used in virtually every industry due to its versatility, precision, and cost-effectiveness for volume production. Medical device manufacturers rely on our injection molding service for components with precise tolerances and biocompatible materials. The automotive sector incorporates molded parts in both interior and exterior applications, taking advantage of their durability and chemical resistance. Consumer electronics products extensively use plastic injection for housings, connectors, and components where consistent quality is essential. Household appliances utilize injection molded parts in everything from handles to internal mechanisms. Parts in the aerospace industry benefit from the lightweight yet strong characteristics of engineered thermoplastics and composites. Packaging solutions, especially those used for food packaging, frequently employ injection molding for containers and closures. The construction industry uses molded parts for electrical components, pipe fittings, and hardware. Injection molded parts are also extensively used in toys, sporting goods, and furniture. Each industry leverages specific aspects of the injection molding process - whether it's the precision, material properties, surface finish options, or economical production of complex geometries.
How does our design for manufacturability (DFM) feedback improve your project?
Our comprehensive DFM feedback is included with every injection molding quote at no additional charge and plays a crucial role in optimizing your design for production success. Our engineers evaluate your part geometry for uniform wall thickness to prevent sink marks, warping, and internal stresses in molded parts. We assess draft angles, which are essential for proper ejection from the mold, typically recommending 1-2° for textured surfaces and 0.5-1° for smooth surfaces. The DFM analysis identifies areas where proper corner radii are needed to reduce stress concentrations and improve how molten plastic flows during the injection molding process. For parts requiring insert molding, where metal components are embedded within plastic, we provide specific recommendations to ensure robust integration. We evaluate gate locations to optimize material flow patterns and minimize cosmetic defects on visible surfaces. Our feedback also addresses considerations for the mold parting line, which affects both aesthetics and function of the finished part. This DFM feedback is used for every injection molding service we provide, helping you avoid costly design revisions and tooling modifications later in the production process.
What materials are typically used in plastic injection molding services?
Our injection molding service offers a comprehensive range of thermoplastic materials to suit virtually any application requirement. Common materials include ABS for its balance of properties, polycarbonate (PC) for transparency and impact resistance, and various nylons (PA) for strength and chemical resistance. Polypropylene (PP) is frequently used for living hinges and food-contact applications. Engineering plastics like polyethylene terephthalate (PET) and polybutylene terephthalate (PBT) provide excellent dimensional stability and electrical properties. For applications requiring flexibility, we process thermoplastic elastomers (TPE) and liquid silicone rubber through specialized molding processes. Many molded parts incorporate glass-reinforced composites to achieve superior strength-to-weight ratios. Material selection considers factors like melting point, moisture absorption characteristics, and chemical resistance required for your specific application. The material choice significantly affects how the mold is designed, particularly for aspects like draft angles and gate locations. When comparing plastic injection molding quotes, it's important to verify that appropriate materials are specified for your application, as material selection impacts both part performance and long-term production costs.
What are the different injection molding processes offered by your service?
Our injection molding service encompasses several specialized processes to address diverse manufacturing requirements. Standard injection molding forms the foundation of our services, where thermoplastic material is melted and injected into the mold cavity to create precise parts with consistent dimensions. For complex components, we offer insert molding, which embeds metal inserts or other materials within the plastic during the molding process, creating robust mechanical connections without secondary operations. Our liquid silicone rubber molding capabilities are used for producing flexible, heat-resistant parts with excellent compression set properties. The injection molding process can be modified for specific applications - we utilize gas-assist injection for hollow parts and structural foam molding for lightweight yet rigid components. Multi-material molding allows us to create parts with different material properties in a single component. Our overmolding process can apply soft-touch grips or gaskets directly onto rigid substrates. Each molding process requires specific expertise in both tooling design and production setup. The molding process selection depends on your part's functional requirements, aesthetic needs, and production volume. Our team provides guidance on the most appropriate injection molding process for your specific application, ensuring optimal results and cost-effectiveness.
How do the lead times compare between prototyping and production molding?
Lead times vary significantly between prototype and production injection molding projects. For prototypes, we typically deliver injection molding quotes within 1-2 business days after receiving complete specifications and CAD files. Prototype tooling, often made from aluminum and designed for limited production runs (1,000-10,000 shots), generally requires 2-4 weeks to produce. The first sample parts are usually available 3-5 business days after tool completion. For rapid prototyping needs, we may recommend 3D printing for initial validation before committing to the injection molding process. In contrast, production tooling designed for high volumes has longer lead times but delivers greater longevity and consistency. Production-grade hardened steel tooling typically requires 4-8 weeks depending on complexity and size. Once the mold is qualified, the first production run needs 5-10 business days for setup, first article inspection, and quality verification. Repeat orders of established production parts usually ship within 5-15 business days, depending on quantity and material availability. Our injection molding service can accommodate expedited production schedules for time-sensitive projects, particularly for customers with established tooling. When comparing molding services, consider both the quoted lead time and the proven track record of on-time delivery, as reliable scheduling is essential for coordinating your overall product development and launch timeline.
What factors determine the cost in plastic injection molding quotes?
Several interrelated factors determine the costs reflected in our injection molding quotes. The most significant initial investment is typically the mold tool itself, with costs varying based on complexity, size, number of cavities, and expected production volume. Material selection substantially impacts per-part costs; standard thermoplastics are more economical, while engineering plastics with specialized chemical resistance properties command premium pricing. Part geometry affects production efficiency – complex designs with varied wall thickness or intricate features require more sophisticated mold tooling and longer cycle times. Production volume is a major cost driver, as higher volumes allow the initial tooling investment to be amortized across more units, significantly reducing per-part costs. The mold design, particularly for parts requiring side actions or multiple cavities, influences both initial tooling costs and ongoing production efficiency. Parts in applications requiring tight tolerances or specific surface finishes may require additional processing steps. Secondary operations such as assembly, pad printing, or specialized packaging add to the overall project cost. Our detailed injection molding quotes break down these components transparently, allowing you to understand the value proposition. For high-volume production, our injection molding service delivers increasingly economical per-unit costs as quantities increase. We provide competitive pricing for both prototypes and production runs while maintaining the quality standards required for your application.